引入数字化研发和制造手段降低成本,是电动车获胜的唯一途径
虽然电车已经发展成熟,但燃油车主还是会更倾向燃油车。如何在在盈利的同时生产出物美价廉并具有长续航的车型是电车制造商将面临的挑战。
海克斯康对416名全球汽车专业人士进行了调查,调查显示,大多数受访者认为,电动汽车会在2026-2028年才能与燃油汽车价格持平。在欧洲和美国,36%的受访者认为直到2028年以后电动车价格才能与燃油车价格相匹配,47%的人确信价格是消费者最大的顾虑,高昂的价格是电动车无法普及的一大障碍。
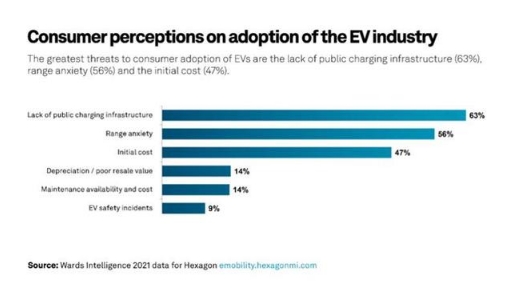
消费者对电动车的期待是提高续航能力(84%)和降低价格(60%),但制造商如何才能平衡这两大需求?增强续航能力意味着投入更多的成本在电池上,同时还需要投入更多成本来减轻车体重量。
尽管疫情使得成本提升,产量变低,但制造商仍选择降低价格来吸引消费者(见图1)并证明了这一决策的正确性。调查还显示,续航问题仍然是消费者的顾虑之一,只有采用续航更长的电池才能解决这一问题,但是长续航电池意味着将大大增加生产车辆的成本。
受访者认为价格是燃油车过渡到电车的最大挑战之一,因此制造商需要考虑如何平衡售价与成本。分析师认为,由于开发成本较高,大多燃油车品牌现在才看到电动车潜在利润。同时解决降低价格、增加利润和延长续航里程冲突需求的唯一方法是提高整个行业的效率。
制造业的悖论式困境是电车购买人数少,使得单价居高不下;研究结果显示,由于电动汽车订单量低,买家无法满足规模经济,供应商也无法实现规模经济。
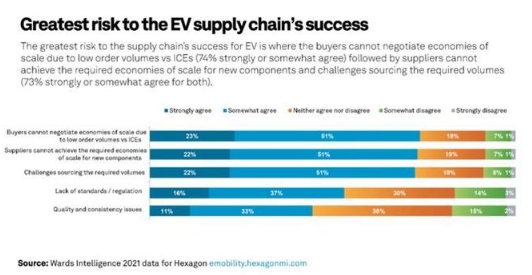
对于传统制造业,提高效率意味着提高产量,提高产量是大型代工厂的根本。但现在的制造商想要缩短上市时间就必须提高效率,提高效率就必须提高零件生产数量,这意味着若使用智能,或数据制造,必须从生产零件开始。
许多代工厂已经使用成本计算功能很多年,包括在前期阶段CAD软件来辅助车间生产。现在工厂的需要更加灵活、协作性强的团队将前期开发和后期组装结合起来同时进行,并驱动数据来快速解决问题。
现在成功的制造商通过使用仿真密集型方式成功地缩短从设计到生产的时间,并证明了虚拟样机的价值,同时他们的创新周期正在缩减。这种生产模式有助于降低车辆成本,同时及时预测并解决潜在的缺陷,以避免不必要的支出和时间上的延误。
法雷奥是此制造原则的一个成功例子,它与海克斯康合作开发了一种新的电力驱动装置,法雷奥的工程师们利用软件迅速得出了多种设计概念,使用现有的部件完成组装,并获得了PACE奖。这种方式采用了模块化设计,开发时间缩短了7-9个月,适用于从电动摩托车和电动自行车到电动汽车的多种应用,有效的降低了制造成本,法雷奥使用此模式将雪铁龙AMI One的上市时间从24个月缩短到18个月。
让各部门一起合作最明显的好处是系统的开发和生产更加一体化,但这样做则需要增加供应链合作和垂直一体化的制造。
"智能制造 "一词经常被用来描述各种利用数据的制造过程,利用数据驱动和机器人生产则需要使开发、生产和组装之间相互连接。
以设计制造变速器为例。开发齿轮的时间可以通过使用质量数据来计算,在芯片开始制造之前就可以开始生产零件,实时计算出来的数据可以提前发现并预防问题的发生。当发现不可避免地问题时,数据便可找出问题所在并追溯到产生问题所在的材料、操作员、机床、工具等。比起原始手写数据,以电子方式传输到机床和检测设备上大大降低了出现错误的概率。
使用数据来预测问题,并通过统计分析来与生产相协调,更加有助于缩小设计理念和产品制造质量之间的差距。
越来越多的制造商开始使用工程合作模式,这种模式大大提升了电动汽车产品的制造效率并提升了制造商的制造水准。例如,美国硅谷的纯电豪华轿车品牌Lucid Motors通过合并各部门同时进行工作的方式,生产出了全新的驱动装置。Lucid将电驱动装置作为一个单一系统进行分析,并让各部门的工程师共同协作,这一方式使公司创造出了市场上最小、最轻、最高效的驱动装置。该73公斤,500千瓦驱动装置由电机、变速器、差速器和反相器组成,此装置具有市场领先的性能。
Arrival是一家英国电车初创公司,它正在开创垂直生产技术和机器人装配,以实现高度自动化的微型工厂,这与传统生产线截然相反。供应商需要实时调动人员,更新系统来满足汽车制造业实时变化的需求,这种方式更像软件公司生产方式。
过去,要想修复在生产过程中暴露出来的设计或软件问题,需要多个部门协作才能定位问题、改进设计、获得批准、进行验证,最后再回到工厂继续生产。这一过程可能持续几周甚至几个月的时间——这种情况现在仍时有发生——但最新的做法是利用更加动态且通常是自动化的方法来解决问题。
过去你绝不会听到汽车公司说“我们在快速迭代“这样的话,但当你考虑到当下电动车的发展速度时,这句话已经变得无比贴切。
汽车制造业想要成功必须拥有灵活性。通过疫情、供应链中断等问题体现出了变化的常态性,现在供应商正在以多种方式解决这些变化。
灵活的制造流程可以满足因产品设计变化而导致的检验需求变化。这种全新模式及确保了产品质量又不会增加额外的劳动力,同时还使产品可以快速上市。
斯科达与海克斯康合作充分的体现了灵活性的好处,该公司使用新型机器人进行编程和控制软件,将编程时间从数天缩短到仅四个小时。该公司为新建工厂配备HxGN机器人进行设备自主检测,同时对现有的生产线进行改造。该软件以运用到车辆部件的设计、检查中。目前,斯柯达汽车公司使用该软件在生产线上更快地部署质量检测环节,以便它们收集新车的生产数据。
电动车频繁的改造要求是制造商最大的挑战之一,由于电车是一个同时包含软件和硬件的“产品”,所以生产电动车需要完善的制造流程。
因此,生产车间和封闭物联网必须进行改造,以创建协作并连接制造流程为目的,从而满足快速组装并及时发现缺少的零件。这样做的前提是机器人和系统必须能够互相联络,才能进行迅速检测和及时纠正故障。
汽车制造商所面临的挑战是如何在电动车世界秩序中取得领先地位,这些挑战既来自业内同时也来自是外界。在目前的订单量下,如果想同时满足价格优惠和更多车型的选择,传统的大批量制造生产线必须被更灵活的制造所取代,才可以加快上市速度。